Fuel remains one of the largest operating expenses for fleet-based businesses; often consuming between 40-60% of total operational costs. In an industry where small inefficiencies add up fast, effective fuel monitoring and full visibility over your fleet’s fuel consumption aren’t just cost-saving measures, they’re key profitability strategies.
At our WhiteLabel Tracking, we equip our clients with tools and insights to run smarter, leaner, and more secure operations. In this article, we’ll explore why fuel monitoring is important, the technologies commonly used today, and the benefits and limitations of each option to help you make an informed decision for your fleet.
Why Is Fuel Monitoring So Important?
Fuel monitoring involves much more than simply tracking liters consumed. In fact, when properly implemented, it helps you:
- Reduce fuel theft and pilferage
- Optimize routes and driver habits to minimize wastage
- Detect discrepancies in refueling activities
- Identify fuel-inefficient vehicles and operations
- Forecast and manage operational expenses more accurately
- Improve fleet productivity and profitability
Without reliable, real-time fuel data, fleet managers are often forced to rely on driver reports and manual logs. Unfortunately, these are prone to errors and manipulation, which ultimately leads to lost revenue and missed opportunities for operational optimization.
Popular Technologies
Modern fleets have access to several fuel monitoring technologies, each with its own strengths and limitations. Let’s break them down:
- Fuel Level Sensors (Capacitive or Ultrasonic Sensors)
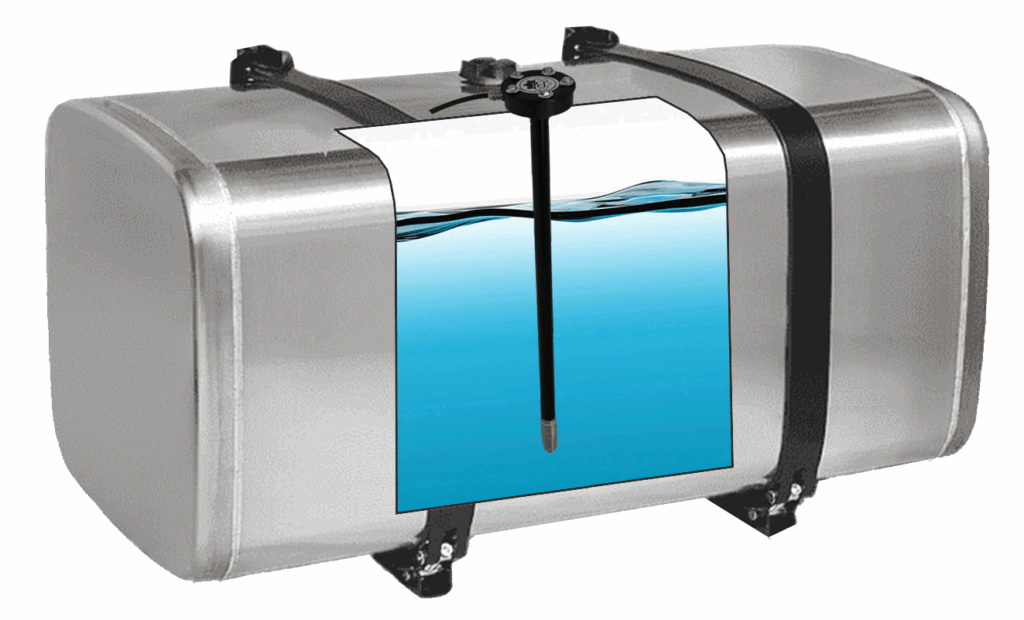
How it works:
Installed directly inside or on top of the fuel tank, these sensors continuously measure the fuel level and transmit real-time data to a central fleet management platform.
Benefits:
- Provides real-time, accurate fuel level readings
- Detects sudden drops in fuel levels (indicating theft or leakage)
- Records refueling events with volume and location data
- Helps establish fuel consumption trends per vehicle
Limitations:
- Requires physical installation and sometimes tank modification
- Can be more expensive upfront, especially for large fleets
- Accuracy may be affected by terrain, vehicle tilt, or fuel sloshing
- Some sensor types have compatibility restrictions with certain tank shapes and materials
- OBD (On-Board Diagnostics) / CAN Bus Data Integration
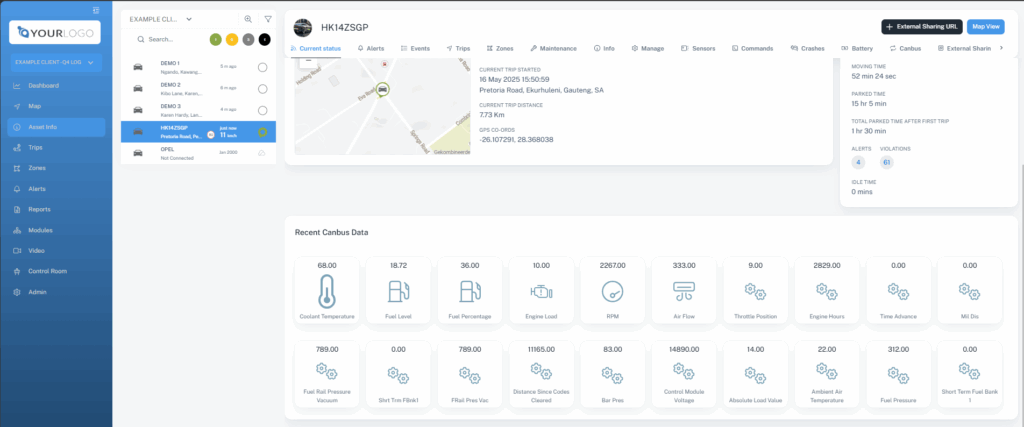
How it works:
Connects to a vehicle’s OBD port or CAN bus system to access engine and fuel consumption data, transmitting it to the fleet management platform.
Benefits:
- Non-invasive installation (via OBD port)
- Provides additional vehicle insights such as engine hours, RPM, and driver behavior
- Cost-effective for light and medium-duty vehicles
- No need for fuel tank modifications
Limitations:
- Less reliable for real-time fuel level monitoring; typically estimates consumption based on fuel usage data
- Not compatible with older vehicles or some heavy machinery without electronic control units (ECUs)
- Data accuracy can vary by vehicle manufacturer and model
- Fuel Gauge Tapping
How it works:
This technique involves connecting a monitoring device to the vehicle’s existing fuel gauge circuit, effectively “tapping” into the sensor signal to estimate fuel levels without installing a separate sensor.
Benefits:
- Cost-effective compared to dedicated fuel sensors
- Quick to install, often using existing vehicle wiring
- Useful for monitoring sudden fuel drops or refueling patterns
Limitations:
- Fuel gauge readings are typically non-linear and imprecise
- Susceptible to false readings caused by vehicle tilt or fuel sloshing
- Doesn’t provide the same level of precision as dedicated fuel sensors
- May require occasional recalibration for accuracy
Comparing the Technologies: Summary Table
Technology | Benefits | Limitations |
Fuel Level Sensors | Real-time level monitoring, theft alerts, refill tracking | Installation cost, terrain influence, tank compatibility |
OBD/CAN Bus Integration | Easy install, broad vehicle insights, affordable for light vehicles | Less precise real-time fuel data, limited on older vehicles |
Fuel Gauge Tapping | Cost-effective, uses existing hardware, quick setup | Inconsistent accuracy, affected by tilt/sloshing, limited precision |
Which Fuel Monitoring Option Is Right for Your Fleet?
The best choice depends on your:
- Fleet composition and vehicle types
- Operational environment (urban, off-road, mixed routes)
- Security risks (fuel theft exposure)
- Available budget
In many cases, a hybrid approach works best:
- Use fuel level sensors on high-value, long-distance, or high-risk vehicles
- Deploy OBD/CAN Bus integration on light and medium-duty vehicles
- Apply fuel gauge tapping where budget constraints exist or for older vehicles without modern electronics
Our fleet management system seamlessly integrates with all three solutions, giving you the flexibility to monitor fuel across a diverse fleet from a single dashboard.
Final Thoughts
Fuel monitoring is one of the smartest investments a fleet operator can make to secure operational profits and minimize preventable losses. No matter the size of your fleet, whether it’s 5 vehicles or 500, accurate, reliable fuel data helps you manage one of your most significant operational expenses.
At Whitelabel Tracking, we’re here to help you design the most effective, cost-efficient fuel monitoring strategy for your fleet; integrating technology where it makes the most impact.
📞 Let’s Talk
Interested in learning how these fuel monitoring technologies could work for your operation? Reach out for a free consultation or request a demo of our integrated fuel monitoring solution today.